〈工業技術與資訊〉電路板產業智慧製造服務應用平台
工業技術與資訊月刊
撰文/陳怡如
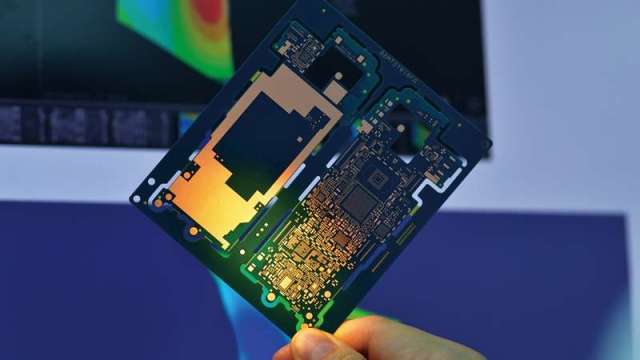
作為全球電路板(PCB)的龍頭,臺灣 PCB 產值已突破兆元。即使擁有完整的上中下游產業鏈,但 PCB 產業仍面臨勞動人口老化、缺經驗與檢測品質的挑戰。榮獲工研院產業化貢獻獎金牌的「電路板產業智慧製造服務應用平台」,透過三大關鍵技術加值,協助產業數位升級,助攻 PCB 產值邁向下一個兆元。
所有電子產品必備的基底板材「印刷電路板」(PCB),堪稱電子產品之母。臺灣 PCB 產業已發展超過 40 年,在去年正式邁入「兆元產業」,產值達 1.04 兆元,更連續 10 年搶下全球龍頭寶座,市占率達 31.4%,在臺灣是僅次於半導體及顯示器的第三大產業。
在輝煌成果背後,挑戰卻悄然而至。工研院機械與機電系統研究所組長王裕銘直指,「臺灣電路板產業正面臨缺有經驗人力,以及檢測品質不均的問題。」根據統計,高達 95% 的臺灣電路板製造商聘請外勞抄表、操作設備,凸顯人力不足的急迫性。且電路板產線長,有多達 2、30 道製程,許多設備操作和參數調整,都須仰賴有經驗的員工。
此外,現有生產和檢測人力的比例約為 1:2 到 1:4,也就是說一個生產人力要配合 2 到 4 個檢測人力。目前業界都以人力檢測,判讀品質因人而異,誤判率也會隨著工時增加、人眼疲憊而升高,影響生產效率及企業商譽。
為了解決產業迫切的挑戰,工研院早在 4、5 年前,便開始打造「電路板產業智慧製造服務應用平台」,以三大核心技術,協助產業朝先進技術、智慧製造升級。
領先國際 建構專屬通訊協定
邁入智慧製造的第一步,首先要建立產業專用的「PCBECI 通訊協定」。工研院機械所副所長周大鑫表示,過去 PCB 的設備和工廠缺乏統一的通訊協定,就像沒有共通語言,設備聯網時資料格式不一,也無法統整傳輸,一直是產業智慧化的瓶頸。
目前國際上最成熟的通訊標準,是半導體業行之有年的 SECS/GEM 通訊協定。團隊以 SECS/GEM 為基礎,依照 PCB 產業需求,重新定義格式並制定訊息封包結構,與台灣電路板協會(TPCA)合作制定全球第一個專屬 PCB 產業的國際通訊協定,包含機台時間設定、事件回報、機台常數資料、遠端控制命令、終端訊息傳送等。在設備聯網時,達到資訊及生產履歷可視化,無須人力抄表。除通訊協定外,工研院也領先全球開發驅動程式,安裝後就能連結通訊,協助產業快速導入,估計縮短 30% 的安裝時程,降低 20% 的維護費用和 40% 的整體成本。
「能夠成為全球第一個推動 PCB 通訊協定的最大原因是,臺灣 PCB 產業夠團結!」周大鑫說。PCB 產業很早就已看到半導體產業制定標準後帶來的效益,加上臺灣又執 PCB 產業牛耳,TPCA 很早就透過產業白皮書來推動智慧製造,因此在 2016 年,工研院和 TPCA 攜手,成立「PCBECI 制定小組」,也希望這個標準能適用於全球 PCB 產業,隔年再跟國際半導體協會(SEMI)提案,經過 3 次全球投票,終於在 2019 年 9 月通過。
肇因分析更聰明 AI 檢測更好用
第二項關鍵技術是「整合式肇因分析模組技術」。透過整合式分析,當產品發生瑕疵時,可回推在生產過程中,造成良率下降或瑕疵的關鍵因子,提供校正建議,或是讓設備自主修正,降低對資深人力的依賴。
「傳統的肇因分析,多僅用單一模型,但是每一種模型都有其條件限制,恐讓判讀失準,」王裕銘表示,這項技術最大的特色是,同時採用多個模型分析,得出每項關鍵因子的排序和占比,讓操作人員在第一時間就能掌握調整的優先順序。
第三項關鍵技術是「AI 影像重繪缺陷分類技術」。將自動光學檢測(AOI)系統拍出來的高畫質影像,經 AI 重繪、濾掉雜質後,直接跟原始設計圖做比對,能更快判斷缺陷,解決人眼判讀品質不均的問題。王裕銘指出,過去要判讀某種缺陷需要千百張、甚至是數萬張的資料去訓練 AI 模型,才能確保準確度,該技術用影像融合方式,所需資料數量可降低 40%,準確率仍可達到 98%。
建立平台 發揮整合優勢
周大鑫表示,過去 PCB 產業導入智慧製造的意願不高,主要在於電路板產業毛利相對半導體業低,投資傾向保守;其次也因為電路板生產流程長,來回修正時,用人力銜接更快。但如今少子化問題嚴重,自動化是必然的路。
「為了提高廠商導入意願,在成本控制上就要更精準,優先選擇廠商最大痛點,讓效益更快浮現,才會擴大導入。」周大鑫補充,在軟體操作上,使用方式及介面也要更友善,尤其中小企業普遍缺乏 IT 能量,以建構平台方式,讓廠商能快速得到軟體支援。
不過這個跨領域整合的平台,初期也面臨不少難題。周大鑫透露,為了整合 PCB 製程、材料、設備、資通訊的人才,「讓大家用共同的語言,的確花了很多時間。」但這個技術最大的優勢也在於「整合」,「我們提供的方案不只是解決某一特定問題,而是建立一個平台,讓不同產業的需求都可以整合輸入,更加全面!」
促成臺灣第一條跨供應鏈的軟板智造產線
完整的平台技術,就像為產業打了強心針,創造亮眼的產業化成效。在制定產業通訊協定上,不僅領先國際,也跟 TPCA 合作促成「PCBECI 設備連網示範團隊」,成功導入聯策等 15 家設備廠,與嘉聯益等 4 家製造商,累計應用套數超過 1 萬套;而電路板產業的設備資訊串聯比例,也由 2017 年的 23.5%,大幅躍升至 2019 年的 48.3%。
該平台還促成兩大研發聯盟,首先是臺灣第一條跨供應鏈的先進軟板智造產線。以垂直產業供應鏈的概念,促成國內軟板大廠與上游材料廠、系統整合商成立研發聯盟,透過設備聯網,讓生產品質資訊跨廠區交流、校正策略分析及缺陷修補。
最終高階軟板良率從 70% 提升至 90% 以上,出貨速度則從 5 天縮短至 0.5 天。相較傳統生產流程,至少可降低 40% 的成本,提高企業獲利能力 30%,並帶動每年約 10 億元的投資,與 31 億元的高階軟板產值。

催化國際級數位智造中心誕生
另一研發聯盟則是促成電路板打樣廠,與設備廠攜手合作。過去國外大廠下單時,會先由廠商打樣,確定設計出來的電路板符合規格再生產,產業特性屬於少量多樣。透過設備智慧化、生產資訊肇因分析、智慧排程等技術,讓打樣廠的交期準確率從 50% 提升至 80%,進而讓打樣業者成為「國際級數位智造中心」,協助多家國際大廠試製,也帶動國產設備廠的設備智慧升級。
王裕銘指出,這兩大聯盟的意義不僅在於讓技術落地,更產生示範效果。他透露,許多廠商看到良率、交貨速度、成本節省都大幅躍進後,紛紛表達合作意願,目前已陸續有載板廠、半導體封測廠、電路板廠前來接洽。
突破日韓壟斷 切入國際供應鏈
這個平台不僅已帶動國內超過 15 家電路板設備廠數位升級,更讓臺廠切入國際供應鏈。傳統印刷設備廠妙印精機,導入 PCBECI 通訊標準和設備數位升級,不良品發生排除時間縮短 6 成以上,同時生產成本也降低超過 6 成、良率增至 96%。為此,妙印更建立智慧製造新創技術部,帶動公司由傳統設備商升級為系統整合廠。
由於生產品質更好、成本更低,讓妙印成功在 2020 年取得泰國第二大電路板廠商的訂單,突破長期被日本及韓國大廠壟斷的困境,搶占新南向市場。未來其他廠商也有機會透過數位升級拿下國際大單。
事實上,除電路板產業外,三大核心技術中,「整合式肇因分析模組技術」與「AI 影像重繪缺陷分類技術」也已實際導入半導體、光學和天線產業,帶動更多產業數位升級,進而扶植臺灣智慧機械產業聚落。
「未來這個平台還會更精進,」王裕銘說,首先,肇因分析目前是生產完了再做回饋,未來希望在生產前就能預測到可能發生的瑕疵;其次,是希望達到設備與設備間的橫向溝通、分析、校正,進一步提升良率。智慧製造是產業趨勢,在疫後 5G、電動車、智慧終端產品需求大增之際,電路板產業產值可望持續增溫,有工研院紮實的技術力做後盾,產業將更具產業韌性與競爭籌碼,持續穩坐全球龍頭寶座。
轉載自《工業技術與資訊》月刊第 353 期 2021 年 7 月號,未經授權不得轉載。
- 從6月延至9月?市場重估聯準會降息節奏
- 掌握全球財經資訊點我下載APP
上一篇
下一篇