〈工業技術資訊月刊〉AI讓工廠產線改頭換面
工業技術與資訊月刊
AI 讓工廠產線改頭換面
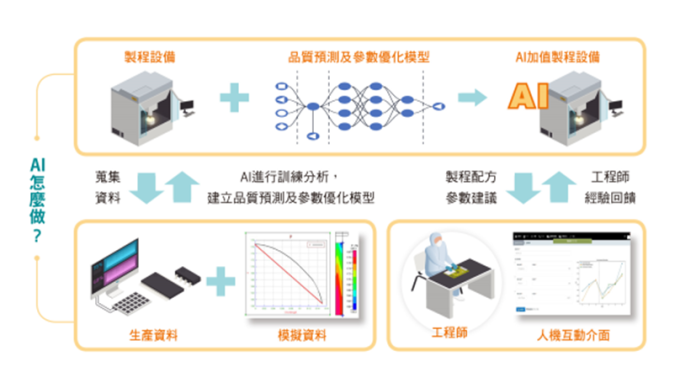
人工智慧(AI)是未來科技的核心,隨著技術逐漸到位,AI 應用也實際在產業付諸實現。製造業出口值占整體出口總值的 7 成,是我國創造外匯的主力,AI 的深度學習技術,大幅精進機器視覺、大數據分析與決策能力,賦予製造業更多的智慧與彈性,不再受限於低價生產成本,進一步吸引製造業回流。
長期以來,台灣以深厚的製造業供應鏈實力睥睨全球,協助眾多知名品牌在國際舞台上發光發熱。然而,東南亞等新興國家崛起,造成全球製造業板塊移動,台灣製造廠商面臨競爭。大量生產與低毛利已不是最具競爭力的獲利模式,如何應用 AI 導入製造業,達到轉型升級、競爭力提升,是製造業此刻最熱門的話題。
台灣科技與傳產製造龍頭不約而同擁抱 AI,希望導入 AI 來提高生產效率、降低成本,然而還有更多的台灣製造業者想問:企業現階段是否該導入 AI?AI 能解決企業哪些問題?提供製造業哪些應用?導入 AI 的挑戰為何?工研院日前舉辦「AI 大未來:技術與應用交流會」,對於上述問題都提供了詳盡的解答。
應邀以「企業數位轉型與 AI」為題發表演說的微軟 AI 研發中心執行長張仁炯指出,企業必須洞察自己的商業核心問題,想清楚自己究竟想做什麼,也可以從客戶端的價值去看,想替客戶帶來什麼價值。他建議,企業可以先從已知的、既存的問題開始,以 AI 的創新方式去解決。換言之,用新技術解決舊問題,可以讓產品或服務獲得更高的商業價值,是企業導入 AI 時應思考的方向。
對製造業而言,品質、彈性與速度是決勝關鍵,在現今講求高效、快速的生產環境下,透過導入 AI,實現少量多樣的生產模式,追求提升營運效率或服務品質。若沒有善用 AI 增加競爭優勢,未來數年可能會面臨業務流失的風險。
設備故障先預知 把搶修變維護
AI 帶給製造業最大的幫助,是讓機器也像人一樣有判斷能力,不僅能自動完成各項製造流程,透過大數據的訓練學習,還能判斷、預測,採取適當的應對。製造設備的預診斷,正是 AI 在製造業可大顯身手之處。
設備無預警停機,會造成整個產線停擺,是製造業的心頭大患,輕則產線上半成品報廢,重則交期延宕影響商譽。根據統計,各產業因意外停機帶來的成本,航空業每秒延遲損失 65 美元;數據中心每分鐘當機損失為 8,851 美元;汽車製造業因生產線停頓,每分鐘損失約 2.2 萬美元;半導體製造業更為慘烈,爐管區乾式幫浦每次停機,損失就高達 12 萬美元。
「如果設備故障前就能提前預知,用維護取代維修,就可以減少停機損失了,」半導體設備廠商帆宣系統科技副總經理韋建名表示,帆宣很早就有研發設備預診斷系統的規劃,為了研發乾式幫浦設備預診斷系統,先後接洽過某知名日商與工研院,工研院的解決方案做出來的資訊分析數據相對準確,甚至還能找到問題所在,讓帆宣十分驚豔,從此開啟雙方合作的大門。
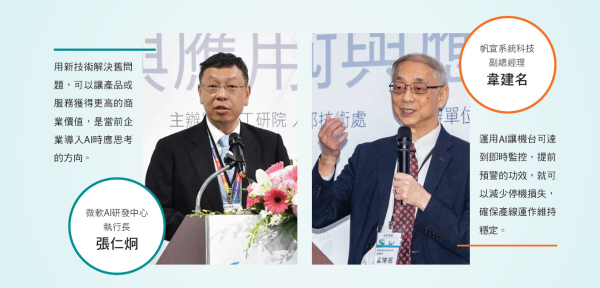
大數據建構預測模型 設備管理輕鬆做
「合作 4 年來,深深感受到工研院扮演了『導師』和『探索性研發』的重要角色,」韋建名說,工研院教帆宣充分了解預診斷相關技術,並竭力協助開發,讓帆宣少走了許多冤枉路,節省很多時間。
帆宣技轉工研院技術後,研發出「基於大數據分析之預診斷系統」,主系統包括設備預診斷、設備生命週期管理、零件生命週期管理、保養與維修管理、決策支援管理、運行即時監控及設備管理等多項子系統,功能相當齊全。
韋建名說明,預診斷系統作業流程包含訓練階段和預測階段等兩大階段,前者先蒐集即時數據,利用先進 AI 學習技術,建置預測模型;後者利用先前建好的預測模型進行預測。如此一來,可降低無預警故障的損失,提供更好的設備零件管理、生產管理,良好的決策支援管理。
半導體或高科技電子產業容不得無預警停機所造成的損失,設備事前診斷功能相形重要,運用 AI 讓機台可達到即時監控、提前預警的功效,對於生產線上遍布精密電子零件的高科技電子產業而言,可確保產線運作維持穩定。
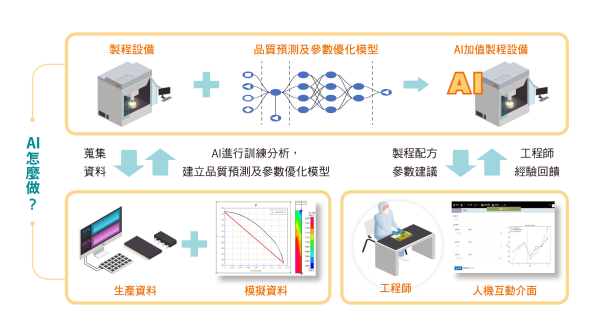
AI 灌頂 配方生成快又好
隨著全球製造業生產技術的迅速發展,如何提高生產良率,已成為降低生產成本及提高產品品質的關鍵指標。以光電半導體製程為例,多需按照客戶的規格,進行製程配方參數的調整。過去製程工程師調整參數時,多憑著領域知識和經驗,但過程耗時、耗力、耗材,工程師的經驗也不易累積成為公司的研發資產,現行製程配方參數研發的作法,已無法滿足產業高效率需求。
工研院研發「製程分析與參數最佳化技術」,採用前瞻資料取樣與實驗設計方法,整合多種先進 AI 演算法,建構製程模型來描述製程參數和產品品質間的關聯,並利用全域最佳化演算法,優化產品品質,快速估測產品品質特性,也可與製程工程師透過互動協作模式,提升研發速度,減少實驗次數,有效縮短先進製程的研發週期、提升良率,加快上市時間。
此基於 AI 的製程分析與參數最佳化技術已實際運用在光電半導體產業,以薄膜製程品質預測為例,可提升品質預測準確度,誤差可降至 21.6%;運用於鋼鐵產業的製程參數優化,則可減少 35% 的實驗次數。
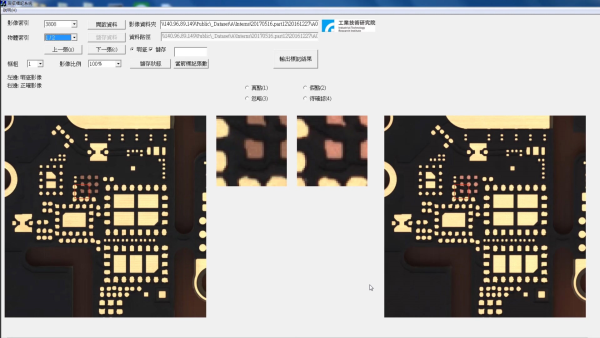
有眼有腦 瑕疵檢測精準高效
良率不高是製造業者的致命傷,不僅增加不必要的成本,更是企業信譽的風險因子。製造業普遍應用自動光學檢測(AOI)設備實現自動化生產流程,但現行設備檢測的正確率不高、瑕疵分類能力不足等問題,容易造成誤判,因此產線仍需仰賴大量人力進行複檢,檢測效率低落。
應用 AI 可讓機器視覺擁有學習能力,解決上述問題。設備導入 AI 將可透過監督式學習演算法,遇到相似的產品種類或瑕疵時,即可自主判斷,不必再由管理人員重新設定、調整判別模式。
工研院的「瑕疵影像分類技術」以深度學習網路架構,並兼具決策彈性與運算效能,瑕疵分類正確率可達 99.95% 以上,可協助目檢員減少 57% 的檢測篩檢量,解決現行生產線仍需仰賴大量人力複檢、效率低落的問題。結合「智慧化資料標記解決方案」,持續強化資料標記品質,降低訓練所需資料標記量至少一半,大幅降低 AI 導入產線應用門檻。
目前工研院已將「瑕疵影像分類技術」導入半導體及 PCB 產業領域。以晶圓廠瑕疵分類為例,運用該技術進行瑕疵檢測的整體正確率大於 97%,高於產業一般所要求的 95%。
自主學習 機器人一夜學會上下料
自主學習機器手臂是製造業邁向 AI 時代的關鍵技術,工研院開發的「機器人自主學習夾取技術」,透過自主學習,可在短短 12 小時學會夾取不同形狀、任意擺放物體的方法,減少人為介入,解決目前工廠換線,須仰賴專業工程師耗時耗力調整機器手臂的瓶頸。AI 機器人讓換線任務更快速、有彈性。
工研院「機器人自主學習夾取技術」以深度增強式學習(Deep Reinforcement Learning;DRL)為基礎,研發自主學習的隨機工件取放料技術,簡單、易用,補足勞力需求。利用 DRL 自主嘗試所蒐集的資料達到最佳的學習結果,提供快穩準訓練機制;並結合機器手臂模擬軟體,在模擬環境進行自主學習,減少整體學習時間和實體手臂嘗試次數。
製造業未來面臨的問題在於少量多樣的挑戰,生產需求變化快速,業者將更頻繁地改變產線內容,以迎合多樣化的需求,這將使機器在導入 AI 時,必須具備更大量的數據資料與更多樣化的學習模式,才能應變瞬息萬變的市場需求。
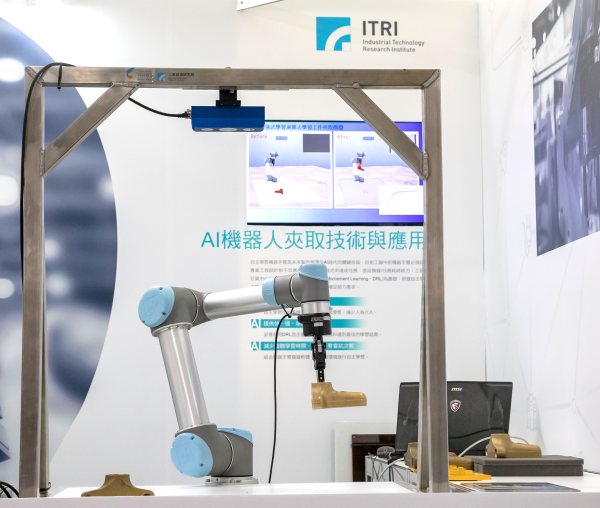
轉載自《工業技術與資訊》月刊第 328 期 2019 年 04 月號,未經授權不得轉載。
- 關稅戰火燒進外匯市場,投資人如何突圍?
- 掌握全球財經資訊點我下載APP
上一篇
下一篇